Available Jobs - Mechanical Engineering / Trades(28)
Hot Jobs
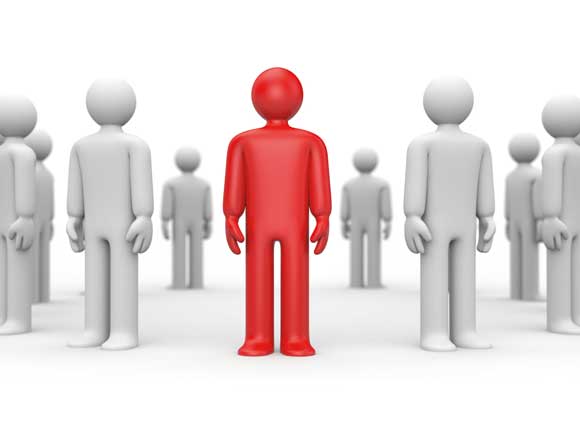
Interview top tips
Available Jobs Mechanical Engineering / Trades
Maintenance of the company fleet - ensure the optimum operation of the fleet by conducting mandatory servicing of every vehicle that arrives and strive to reduce the number of breakdowns
Coordinating with stores staff to ensure that the required spares for maintenance/ repair work are on hand and immediately available to undertake works as and when they are needed
Supervision of workshops staff to ensure all teams execute to meet laid down deadlines and maximize their performance
Ensure the truck dispatch forms are correctly signed off and works counterchecked so every fault reported by a driver is correctly reported and worked on
Ensure that teams are assigned with vehicles throughout the day to ensure works are undertaken on all trucks
Ensure all drivers leaving the yard are debriefed on works undertaken on their trucks and signed off accordingly
Maintenance of workshop and workshop and workshop equipment - to ensure adequate use and maintenance of tools, equipment and other materials in the workshop
Ensure zero idling of workshop staff and every workshop staff is working on assigned vehicles
Administration - to ensure the creation and maintenance of record keeping system (manually and electronically) that covers a trail of all trucks worked on spares requested for by fully completed in job cards and demand sheets that filed systematically that can be requested with ease at any time
Ensure all scrapped cores are taken into stores for insurance of replacement parts
Ensure any near misses and accidents in workshops are reported to Management and all relevant reports updated for review
Ensure all team members are reminded of HSES compliance and ensure stores is updated of any, missing or damaged workshop PPE to same is urgently reported
Responsible for promoting and maintaining a safe work environment at all times and inspecting equipment for safety compliance and reporting any unsafe equipment tools or practices
Fully adhering and strictly complying with all HSE Manuals, guidelines and memos
Any other duties as delegated by management
Required Skills
Technical
Strong leadership skills
Experience with welding and hydraulics
Additional Requirements
Directly supervises employees in the performance of their duties, which may consist of Electro-Mechanics, Electricians, Maintenance Men, Maintenance Helpers, Lubrication Men and Welders
Assignment of work as required by priority and schedule, and to perform this work at a minimum cost
Audit work methods, provide guidance and training for employees
Make recommendations for improvement to the department's performance and efficiency
Review and use backlog reports, downtime reports and budget reports as a management tool
Maintain control of company policies, safety regulations, housekeeping and operating standards
Participate in the Confined Space Rescue program, which includes training, meetings, drills and rescues
Prepare reports and maintain records as are required in the performance of his duties
Perform any other related duties as assigned by his Supervisor or higher authority
Initiate construction specifications
Required Skills
Prior experience in a supervisory role.
Experience with construction.
Excellent project management skills.
Good interpersonal skills.
Excellent leadership skills.
Additional Requirements
Design or implement programs and strategies related to water resource issues such as supply, quality, and regulatory compliance issues
Perform hydrologic, hydraulic, or water quality modeling.
Analyze storm water systems to identify opportunities for water resource improvements.
Conduct, or oversee the conduct of, investigations on matters such as water storage, wastewater discharge, pollutants, permits, or other compliance and regulatory issues.
Required Skills
product and service design development knowledge
Safety and legal knowledge
Problem Solving
Visual Understanding
Integrity
Analytical Thinking
Attention to Detail
Dependability
Initiative
Achievement/Effort
Additional Requirements
Assigns jobs and supervises subordinates on daily work activities as specified on the work orders.
Coordinates servicing of all electrical components on yellow machines, light vehicles, tractors and HOWO trucks.
Monitor rewiring of all vehicles.
Delegate to subordinates the switching on and off of generators immediately when there is no electricity.
Monitor the installation of GPS on all tractors.
Ensures good housekeeping of work areas all times
Expedites orders (vehicle components)
Required Skills
A team player with good communication skills
Highly knowledgeable in today’s automotive technology to include, computer diagnostic machines for a variety of vehicles including light motor vehicles, yellow machines, tractors and buses
Additional Requirements
Duties & Responsibilities
The Workshop Technical Manager manages the Technical dimensions of Workshop, which is made up of: inspection bay, main workshop bays, trailer section, breakdown section, sandblasting and spray painting, panel beating, truck breakdown area, wash-bay and workshop administration (herein is referred to as “the workshop”). It is the Workshop’s responsibility to maintain the fleet which includes: rollers, motorbikes, generators, tankers, trucks, trailers, light vehicles and any other machinery and or vehicles used by the company.
Outline of Duties & Responsibilities:
? Manage the Technical area of the Workshop;
? Ensure that the fleet is maintained and serviced, and kept in safe and working properly;
? Coordinate and liaise with the Procurement and Stores Supervisor to ensure spares stock levels are maintained to support the fleet and the appropriate spares and consumables are being used;
? Inform Stores & Procurement about spares needed, in sufficient detail to ensure the spares purchased meet manufacturers and company specifications;
? Ensure all Job Cards are closed with the appropriate information captured.
? Adhere to all standard operating procedures (SOP) provided by the manufacturer of the machine/vehicle or its agent;
? When necessary, test drive vehicles to ensure that they are functioning appropriately, and arrange a driver for vehicles requiring a special driver;
? Assist the Workshop Administration Manager to maintain and manage fleet records in FMS including advising which vehicles should move between fleets and ensuring that the physical vehicle matches with the record on FMS;
? Assist and advise senior management on disposal of fleet assets whether by selling or writing off;
? Assist and advise senior management on acquisition of new fleet assets;
? Reduce costs and waste by increasing the use of used parts;
? Promote compliance with HSES registers and housekeeping rules, by regular briefing and toolbox talks.
? Ensure the appropriate usage and handling of testing tools and repair equipment;
? Assist operations and legal departments whenever required, particularly in accident evaluations, quotations, driver and/or workshop deductions relating to misuse or damage of equipment;
? In conjunction with the documentation department ensure vehicles have a valid VID;
? Manage, supervise, support and develop the Workshop team, ensuring a high level of motivation, discipline and morale is maintained;
? Ensure that new employees are hired in line with recruitment policy and are trained and educated according to the company standards and safety requirements;
? Ensure attendance is regular and report any irregular situation to HR and/or legal departments, in order to take corrective actions and/or disciplinary processes in line with company policies and labour law;
? Manage and report on any employee assigned to assist outside the workplace (i.e. breakdowns, port incidents, etc), in order to keep time records in accordance with the regulations in force and to ensure effective breakdown management;
? Ensure that all workshop accidents are reported and investigated in accordance with the regulations in force and liaise with the legal and HSE teams regarding accidents;
? Perform other tasks as may be required by the Workshop Admin Manager and General Manager.
Required Skills
? Good inter-personal skills and ability to work in a team;
? Good judgment and strong profit orientation;
? Display high levels of responsibility and accountability;
? Hard worker, with high levels of energy and self-motivation;
? Planning and organization skills;
? Decision making skills;
? Able to establish and maintain effective working relationships with subordinates, co-workers, managers, suppliers and general public;
? Conflict management ability;
? Pro-active management style with initiative, dynamism and assertiveness approach;
? Show interest in developing staff who directly report to the manager;
? Ability to ensure compliance with the Health, Safety, Environmental & Security and Anti-Bribery and Anti-Corruption policies for the manager and staff directly reporting to said manager;
? Available to pursue personal development of skills and knowledge necessary for the effective performance of the role
Additional Requirements
Outline of Duties & Responsibilities
Assessing a vehicle’s damaged panels and components, either by cutting them away or unbolting them from the vehicle
Replace the damaged parts or repair them, using mechanical, hydraulic and metal working equipment
Rejoins repaired parts with welding equipment and repairs dents with plastic fillers and file
Grinding, sanding, repainting and polishing the vehicle after repair
Repairing chips and scuffs, polishing and waxing, glass repairs, interior repairs and wheel refinishing
Performing all necessary maintenance and repair on all equipment used in panel beating
Responsible for maintaining a well organized area in compliance with all company polices and guidelines
Ensure work area is clean at all times
Perform other tasks as may be required by the Workshop Foreman and/or Workshop Manager
Required Skills
Display high levels of responsibility and accountability
Hard worker, with high levels of energy and self-motivation
Able to establish and maintain effective working relationships with subordinates
Willingness to work nights and weekends as per workload
Additional Requirements
Diagnose rig electrical and hydraulic problems.
Ensure work is performed to comply with company appropriate standards.
Interpret manuals and identify rig and tractor spare parts and liaise with the Operations Manager in regard to parts ordering.
Correctly use and maintain all personal protective clothing and equipment supplied by the company.
Carry out servicing, maintenance and repairs to rigs and tractors as directed by the Operations Manager or Supervisor.
Diagnose faults in rig and tractor systems and rectify.
A proven commitment to workplace Health and Safety.
Undertake other duties which are relevant to the position as requested by the Operations Mnaager.
Required Skills
Additional Requirements
Key Performance Areas
Formulating maintenance programmes in accordance with World Class Operations practices and implementation thereof - ensuring high plant/equipment availability and reliability at all times.
Co-ordinating the provision of Engineering Services to user departments, ensuring the right quantities and quality at all times in a sustainable manner.
Scheduling and management of all CAPEX projects and co-ordinating the implementation thereof timeously and cost effectively.
Developing and implementing appropriate Training and Development plans for Engineering Staff.
Drawing the Engineering budget, ensuring effective implementation and controlling expenditure.
Full responsibility for the day to day management of the Engineering Department.
Engagement and management of all stakeholders.
Required Skills
Effective leadership and management skills.
Ability to work and make sound decisions under pressure.
Highly computer literate.
Additional Requirements
Duties to include:
To install, troubleshoot, repair, upgrade, service and maintain electrical and mechanical equipment
Required Skills
Honest and trustworthy
Have initiative and be able to work without supervision
Additional Requirements
Reading, interpreting and development of concept Engineering drawings.
Fabrication and Welding of Plating, Piping, Ducting, Development, Structural and Installation
Attend to breakdowns and new mechanical installations
MMA, MIG, FCAW Open ARC, Oxy Acetylene Welding and Cutting, Plasma Manual and CNC Processes
Material Quantification, Consumable and Labour Estimations
Labour Training, Skill Development and Project Planning
Required Skills
Team Player
Additional Requirements
Communicates directly with General Manager to ensure effective participation by the maintenance technicians in the implementation of autonomous maintenance and preventive maintenance schedules.
Assists with planning and implementing plant improvements and expansions in conjunction with the General manager.
Maintains and updates operating and training manuals for the maintenance department.
Updates General manager of all maintenance work and projects going on the farm with the use of the maintenance schedule and a projects schedule.
Reviews the operation of plant equipment and systems constantly, to minimize unplanned downtime, anticipate solve problems in a timely manner, and to identify opportunities for improvement.
Identify machines which are obsolete and would prove costly to maintain or repair, for disposal.
Ensures that maintenance technicians are adequately trained, equipped, and motivated so that the maintenance program can be accomplished in a safe, timely, and cost-effective manner.
Monitors the use and inventories and makes reports of spare parts, maintenance supplies, and equipment and initiates reordering when necessary.
Directs, maintains, and enforces the safety program for the maintenance department; reviews safety records to uphold standards of maximum safety for all maintenance technicians.
implement cost effective, time-based projects with World Class Engineering/parts and ensure all projects meet their deadlines and are within their budgets
Ensure zero accidents.
Act on reported accidents or incidents immediately they happen.
Active participation and ensuring compliance of activities.
Ensure progressive Training in the department
Continuous Improvement skills
Weekly update/ follow up meeting with General manager and maintenance team. Completes the labor budget.
Oversees the Preventive Maintenance Program.
Oversees maintenance work orders.
Oversees the facility and the equipment inside and outside.
Oversees contractors.
Oversees production downtime.
Oversees the pre-op lockout and tagout program.
Makes sure that facility drawings are updated.
Looks for improvements to be made in plant utilities.
Oversees safety programs.
Performs and oversees training programs.
Works with and assists in monitoring the purchase of parts and equipment to maintain the facility.
Required Skills
Project management
Content development
Creative approach to work
Strong Attention to Detail
Ability to Work Without Supervision
Excellent Time Management Skills
Additional Requirements
Purpose of Role:
Provide excellent customer service, product knowledge and technical expertise to all internal and external customers and employees of the company. Support the Technical team to meet deadlines, business objectives and the customer's needs in relation to products and service. Ability to quickly identify and escalate significant technical issues and develop positive solutions to complex challenges. Ensure Goods Received Advice notifications are processed in an accurate and timely manner, together with providing quality customer liaison and query handling, in accordance with company procedures.
Key Accountabilities
Engineer and modify bills of material according to data sheet/ order
Loading of materials and purchase items for pump projects on SAP
Liaise with the drawing office
Supply data to draughtsman and ensure drawings are in accordance with the data sheet specifications, expedite drawings from draughtsman
Handle internal queries from sales, purchasing and production departments
Ensure the efficient and effective engineering of all non — standard bills of materials and their associated functions
Enter non-standard and standard jobs on to SAP system
Complete customer project documentation
Handling all queries from customers/suppliers
Planning
Read, check and generate drawings/ documents
Attend to enquiries
Update and check IMN's
General enquiries with suppliers
Verify pump and material selection, performance, mechanical seal selection and auxiliaries
Comply with and enforce all KSB policies and procedures
9 Assist fellow employees with daily functions as and when required
Carry out all other reasonable tasks that may be delegated from time to time
Required Skills
• Committed to customer care,
• Ability to work under pressure,
• Mechanically minded,
• Positive can do' attitude,
• Ability to meet deadlines
Additional Requirements
The candidate needs to come from the pumps industry with knowledge of water & surface pumps combined with the ability to drive sales & focus on customer satisfaction The role involves Warehouse Management, Sales Management as well as Inventory and Procurement Management.
Required Skills
Ability to strategize and plan ahead.
Excellent verbal and written communication skills.
Additional Requirements
Marking out, fabricating and welding of high-pressure pipes and vessels from drawings and on-site designs.
Using a variety of welding techniques and machinery (CO2, Argon welding MIG and TIG).
Conducting and participating in Risk assessments for all jobs at hand.
Completing job cards and description of work as per instruction or as from Planned Maintenance (PM) Office.
Required Skills
Must be familiar with risk assessment procedures
Additional Requirements
Details of work that needs to be carried out on all cars present
Tracking lead times
Communicate with Parts division regarding the essentials that need to be on hand to reduce delays
Review the effectiveness of the work carried out
Confirm the details of the required work that needs to be carried out
Put in place staff development plans
Very detailed knowledge of investigating the problems that need to be identified before quoting can be carried out
Communicating with the Parts Division Manager to reduce delays and present details to improve the way forward
Will report to the Dealership General Manager
Oversee all Workshop activities (parts, service plans, staff development, delays, improvement plans).
Required Skills
Technical Skill
Leadership Skill
Additional Requirements
Typical tasks include:
assembling, fitting and repairing tools
following engineering drawings to measure and mark out the design for the tool
using hand tools such as files, hacksaws and grinders
using machinery such as lathes, presses, milling machines and grinders to cut and shape the tools
using precision measurement instruments such as micrometers, gauges and vernier calipers to check the tool’s dimensions
monitoring the tools used on the manufacturing line to ensure efficient run rates and identify necessary repairs or possible improvements
attending machine breakdowns to identify the root cause and solve the problem
assisting with tool maintenance
compiling reports
Required Skills
Good hand-to-eye co-ordination
Attention to detail
Accuracy
Good verbal and written communication skills
The ability to work independently and as part of a team
Additional Requirements
Duties to include
Welding
Steel fabrication
Required Skills
Additional Requirements
Ensure excellent customer service
Liaise with Senior Management as to all Maintenance and repair requirements.
Implement and control all maintenance procedures that pertain to all vehicles
Schedules maintenance and repairs for the workshop.
Ascertains and advises on spare parts levels and maintenance scheduling that are required to attain maximum vehicle availability.
prepare planned maintenance schedules for all vehicles.
Maintains Job Card discipline and adheres to processes.
Final sign off on all job cards
Ensure all safety standards and practices are strictly adhered to.
Liaise with all Office managers and field mechanics as to their maintenance requirements.
Ensures tools are present and correct, ensures future tooling requirements are being met.
Ensure maintenance and inspection of all workshop equipment and tools.
Ensure all maintenance personnel are receiving the correct training in all aspects of their jobs.
Oversee quality of all mechanical work and ensure safety procedures are followed thoroughly.
B) SUPERVISORY DUTIES
Identifies the training needs of immediate subordinates, recommends training for them, and ensures that staff of the department receive appropriate training.
Appraises the performance of immediate subordinates.
Reviews the performance appraisal reports on all staff in workshops.
Recommends promotion, transfer and engagement of staff in workshops.
Recommends to Operations Support requisition of materials and spares.
Ensures that all reports subscribe and adhere to planned maintenance procedures.
Ensures SHEQ program is adhered to.
Ensures productivity is maximised and exceeds targets.
Ensures work is carried out within planned time frames.
C) OTHER DUTIES:
Perform all duties that are assigned by the company Directors at his discretion
Required Skills
Additional Requirements
Duties and Responsibilities include but are not subject to:
Actively collect and give feedback on market information about tyre performance and competitor data
Ensure that a high level of customer satisfaction is provided for the service and support to our customer fleets
Provide a high level of hands -on service and technical advice for customers
Required Skills
A good understanding and basic working knowledge of MS-office, good communication skills and interpersonal skills.
Quick to learn new skills, technical information and concepts about tyres.
Additional Requirements
Typical tasks include:
assembling, fitting and repairing tools
following engineering drawings to measure and mark out the design for the tool
using hand tools such as files, hacksaws and grinders
using machinery such as lathes, presses, milling machines and grinders to cut and shape the tools
using precision measurement instruments such as micrometers, gauges and vernier calipers to check the tool’s dimensions
monitoring the tools used on the manufacturing line to ensure efficient run rates and identify necessary repairs or possible improvements
attending machine breakdowns to identify the root cause and solve the problem
assisting with tool maintenance
compiling reports
Required Skills
Attention to detail
Accuracy
Good verbal and written communication skills
The ability to work independently and as part of a team
Excellent math and IT skills
Additional Requirements
Repair and maintenance of agricultural equipment
Diagnosis and repair of machinery
Replacement of parts or upgrading of outdated components
Required Skills
Experience with Electronic Servicing Tools
Experience with agricultural, mining or construction equipment
Additional Requirements
Responsibilities include but are not limited to
Diagnosis, repair & installation of equipment, including pre-shift maintenance
Basic welding techniques in a non-structural engineering format
Complete job cards, time sheets, material requisitions, attendance register
Required Skills
Ability to work under pressure
Additional Requirements
Not only do machine shop Operations Managers oversee fabrication activities, they manage costs and expenses through process efficiencies.
Managers make sure the proper equipment is on hand and ready to meet production demands.
Job duties require you to analyse and adjust work schedules, solve production problems, handle quality issues and manage customer interactions.
Personnel matters will also be your responsibility.
You must plan for employee training and skill development and handle disciplinary issues. Making sure operations align with company policies and procedures is also part of the job.
Required Skills
You need excellent communication skills and the ability to work with customers, suppliers and employees across all levels, including sales and marketing, engineering, maintenance and human resources.
You need a thorough understanding of machining processes, equipment technology, shop procedures and how to read drawings.
Knowledge safety and health regulations with regard to safe use of machine tools is also necessary. Successful work as an Operations Manager typically requires hands-on experience.
You need to have experience in a machine shop, working with machine tools or worked in an engineering field.
Consideration will be given if you have a combination of mechanical skills and work experience.
Additional Requirements
Contributes to the creation and implementation of best practice, maintenance vision, strategy, policies, processes, and procedures for the company.
Effectively delegates any maintenance issues to the skilled and semi-skilled artisans.
Develops a Planned Preventative Maintenance (PPM) schedule; ensure full preventative maintenance is carried out.
Ensures that designated buildings, plant, and facilities are fit for purpose and to provide proactive support/solutions when required.
Develops clear accountability for maintenance material spends combined with a strategy to manage expenditure.
Ensures that the function operates in accordance with any health, safety and environmental policies and procedures to ensure the safety and wellbeing of staff and visitors.
Manages, coaches, and develops a high performing maintenance team that meets agreed objectives, and which delivers best practice results, added value and continuous improvements.
Sets departments objectives/KPIs and review and assess ongoing performance of direct reports.
Manages and leads the team, ensuring adequate staffing levels.
Develops and maintains strong relationships with internal and external stakeholders to ensure optimal work collaboratively negotiate and engage with key stakeholders to facilitate delivery and compliance with the maintenance strategy.
Conducts performance reviews.
Manages all engineering company projects.
Liaises with purchasing in sourcing of spares.
Required Skills
Additional Requirements
Engage with local commercial farmers to promote company agricultural contracting services
Utilize computer software to create plans and detailed blueprints
Troubleshoot problems that may come up during the agricultural season
Scheduling of daily workflows
Monitor daily productivity of contracted equipment
Set daily work programmes
Ensure compliance with Health & Safety standards
Required Skills
Mechanical knowledge of heavy plant, generators and tractors. Personal Qualities
Good planning and activity scheduling skills, technical skills and a hands-on approach
Able to communicate at all levels
Ability to work effectively with people of different cultural backgrounds
Must be self-motivated and results driven
Capability to work under strict deadlines
Ability to work with minimum supervision
Team player
Client liaison skills
Additional Requirements
Able to take over smooth operations of the workshop.
Responsible for planning, job allocation and job flow in the workshop and on site including job scheduling and labour allocation for day to day operations.
Leading and motivating a team of mechanics, technicians, and workshop staff
Manage costs for repairs and spare parts in the interest of the company
Required Skills
Focused and Driven
Excellent leadership and communication skills
Strong creative thinking and problem solving skills
The ability to work under pressure and handle stress
Additional Requirements
Conduct regular maintenance on machinery, systems, and automotive vehicles.
Meet with clients to better understand their concerns and identify the issue.
Assemble mechanical components according to specifications.
Examine machines and oversee diagnostic tests to determine functionality problems.
Design a plan of action for all maintenance tasks and upgrades.
Maintain work logs, repairs, and maintenance records.
Monitor inventory and order new parts when necessary.
Offer consultation on maintenance and preventative procedures to machine and vehicle users.
Perform vehicle assessments
Required Skills
In-depth knowledge of Case Equipment is essential
Knowledge of vehicle diagnostic equipment and mechanical systems.
Strong attention to detail with an aptitude for problem-solving.
Excellent communication skills.
Additional Requirements
Designing, manufacturing, maintenance and installing components that fulfill requirements.
Analyzing problems or deficiencies and developing solutions to resolve them.
Conducting experiments and evaluations to improve and innovate product designs.
Creating plans and designs using CAD technology.
Estimating budgets and time scopes for each project.
Writing technical documentation for machine operators.
Ensuring that products meet compliance regulations.
Collaborating with project managers and other engineers in our team.
Required Skills
Ability to run simulations and analyze test data.
Ability to write clear and comprehensive technical documentation.
Highly analytical mind, with exceptional problem-solving skills and attention to detail.